Non-Destructive Testing (NDT) in Koraput
Non-Destructive Testing (NDT) in Koraput, is the process of inspecting, testing, or evaluating materials, components or assemblies for discontinuities, or differences in characteristics without destroying the serviceability of the part or system. In other words, when the inspection or test is completed the part can still be used. In contrast to NDT, other tests are destructive in nature and are therefore done on a limited number of samples rather than on the materials, components or assemblies actually being put into service.
These Non-Destructive Testing (NDT) in Koraput are often used to determine the physical properties of materials such as impact resistance, ductility, yield and ultimate tensile strength, fracture toughness and fatigue strength, but discontinuities and differences in material characteristics are more effectively found by NDT.
Increased Safety: By avoiding the need to cut or destroy a material or component, NDT reduces the risk of accidents and injuries in the workplace.
Cost-Effectiveness: Non-Destructive Testing (NDT) in Koraput can be a more cost-effective way to test and inspect materials and components, as it does not require the costly replacement of materials that would be destroyed during testing.
Increased Efficiency: NDT can be done quickly and efficiently, allowing for rapid results and minimal disruption to production or manufacturing processes.
Versatility: Non-Destructive Testing (NDT) in Koraput can be used to test a wide variety of materials, including metals, composites, ceramics, and plastics, and can be used to detect a range of defects and issues.
Continuous Monitoring: NDT methods like ultrasonic testing, radiographic testing, eddy current testing etc can be performed in situ, online on a component while it is in service so they can detect defects or changes in properties.
Increases Reliability: Non-Destructive Testing (NDT) in Koraput allows for detection of defects, which can result in a more reliable product and a reduced risk of failure.
Inspecting for internal defects in metals, such as cracks, porosity, and inclusions.
Evaluating the integrity of welds in pipelines, pressure vessels, and structures.
Detecting corrosion and erosion in metal structures and equipment.
Checking the thickness of metal parts and coatings.
Examining the quality of concrete and other construction materials.
Evaluating the condition of aircraft components, such as fuselage, wing structures and engine components.
Inspecting the structural integrity of bridges, buildings, and other structures.
Monitoring the performance of industrial equipment such as power generation plants, refineries, and chemical processing facilities.
Quality control in manufacturing industries, aerospace, automotive, medical devices and equipment, etc.
Non-destructive testing (NDT) in Koraput method can be visual testing, ultrasonic testing, radiographic testing, magnetic particle testing, liquid penetrant testing, eddy current testing, acoustic emission testing, and others depending on the need and materials being inspected.
These Non-Destructive Testing (NDT) in Koraput are often used to determine the physical properties of materials such as impact resistance, ductility, yield and ultimate tensile strength, fracture toughness and fatigue strength, but discontinuities and differences in material characteristics are more effectively found by NDT.
What is Non-destructive testing (NDT)?
Non-destructive testing (NDT) is a group of testing and analysis techniques used to evaluate the properties of a material, component, or system without causing damage. These techniques are used to find defects, measure material thickness, and determine the mechanical properties of a material without altering the integrity of the material being tested. There are various types of NDT methods like visual inspection, radiographic testing, ultrasonic testing, magnetic particle inspection, liquid penetrant inspection, eddy current testing etc. These methods are used to inspect and test a wide range of materials, including metals, composites, ceramics, and plastics, and are used in a variety of industries, including aerospace, manufacturing, and construction.There are Several Benefits of Using Non-Destructive Testing (NDT) in Koraput, which include:
Preservation of the Integrity of the Material or Component Being Tested: NDT allows for testing and analysis to be done without causing damage, so the material or component can continue to be used afterward.Increased Safety: By avoiding the need to cut or destroy a material or component, NDT reduces the risk of accidents and injuries in the workplace.
Cost-Effectiveness: Non-Destructive Testing (NDT) in Koraput can be a more cost-effective way to test and inspect materials and components, as it does not require the costly replacement of materials that would be destroyed during testing.
Increased Efficiency: NDT can be done quickly and efficiently, allowing for rapid results and minimal disruption to production or manufacturing processes.
Versatility: Non-Destructive Testing (NDT) in Koraput can be used to test a wide variety of materials, including metals, composites, ceramics, and plastics, and can be used to detect a range of defects and issues.
Continuous Monitoring: NDT methods like ultrasonic testing, radiographic testing, eddy current testing etc can be performed in situ, online on a component while it is in service so they can detect defects or changes in properties.
Increases Reliability: Non-Destructive Testing (NDT) in Koraput allows for detection of defects, which can result in a more reliable product and a reduced risk of failure.
Non-Destructive Testing (NDT) in Koraput is Used for
Non-destructive testing (NDT) in Koraput is a wide range of analytical techniques used to evaluate the properties of a material, component, or system without causing damage. Some common applications of NDT include:








Non-destructive testing (NDT) in Koraput method can be visual testing, ultrasonic testing, radiographic testing, magnetic particle testing, liquid penetrant testing, eddy current testing, acoustic emission testing, and others depending on the need and materials being inspected.
NDT IN CONCRETE
REBOUMD HAMMER TEST



Objective of Test:
Rebound Hammer test could be used for:-



ULTRASONIC PULSE VELOCITY



Objective of Test:
Ultrasonic Pulse Velocity test could be used for:





CARBONATION TEST
What is Carbonation?
Carbonation occurs in Concrete because the calcium bearing phases present are attacked by carbon dioxide of the air and converted to calcium carbonate. Cement paste contains 25-50 % calcium hydroxide Ca (OH)2, which mean that the pH of the fresh cement paste is at least 12.5.

Objective of Test:
The phenolphthalein test method is intended to measure the depth of the carbonated layer near the surface of hardened concrete. It is not suitable for concrete made with calcium aluminate cement. It may be used on site or in the laboratory, on test specimens or on cores or fragments removed from hardened concrete structures.
NDT IN METAL
ULTRASONIC TESTING



ULTRASONIC THICKNESS TESTING

DYE PENETRANT TEST

Inherent: Ingot discontinuities such as Solidification cracks and porosity; Casting discontinuities such as Porosity, Shrinkage, Hot tears and Cols shuts.
Primary processing: Cracks that occur during welding, straightening, bending, or processing such as heat treatment, plating, and grinding that are caused by internal tensions. inclusions with surface opening and porosity in welds. There are laminations visible near the plate's edge. In the forging and forming processes, there are gaps, seams, bursts, and cracks. In-service Service cracks brought on by overloading, wear and tear, or corrosion are discontinuities.
MAGNETIC PARTICLE TESTING

Locally or globally, the test sample is magnetic. A surface-breaking flaw will distort the magnetic field and lead to flux leakage all around it. Very small iron particles that are placed dry or floating in a liquid cause the leakage flux to be visible at the surface. The areas of flux leakage, which are visibly visible, are where the particles gather. An iron powder line on the surface, then, indicates a crack or fault.
RADIOGRAPHIC TESTING
A detecting agent is needed to create a visible image because X and Gamma Rays are invisible. The radiographic film in light-resistant packaging or a digital image sensor can serve as this detecting agent. When the film is developed, the parts of the sensor that have been exposed to more light appear dark. The oil and gas, aerospace, transportation, military, automotive, manufacturing, and power industries all frequently use radiographic testing.
Non-Destructive Testing (NDT) in Koraput is an expensive technique compared to the other non-destructive techniques and is permanently used to defect internal flaws in casting and elements.
This method uses penetrating gamma- or X-ray radiation to analyse the components and finished goods for flaws, which are shown as the density changes in the film, much to how an X-ray reveals fractured bones. For all of the materials made at Brechmann-Glass, it serves as the standard test method for identifying internal flaws. By using industrial radiography and X-ray technologies, virtually any material may be examined for internal flaws. Industrial radiography, which uses electromagnetic waves with wavelengths in the manometer range and frequencies between roughly 1017 and 1022 Hz, deals with very energetic, very short-length waves.



This method uses penetrating gamma- or X-ray radiation to analyse the components and finished goods for flaws, which are shown as the density changes in the film, much to how an X-ray reveals fractured bones. For all of the materials made at Brechmann-Glass, it serves as the standard test method for identifying internal flaws. By using industrial radiography and X-ray technologies, virtually any material may be examined for internal flaws. Industrial radiography, which uses electromagnetic waves with wavelengths in the manometer range and frequencies between roughly 1017 and 1022 Hz, deals with very energetic, very short-length waves.
Click Here To Download-NDT Testing Broucher -
Why Choose National Building Material Lab (NBML) for Non-Destructive Testing (NDT) in Chhattisgarh?
At NBML, we're your trusted partner for Non-Destructive Testing (NDT) in Chhattisgarh. Here's why you should choose us:
- 1. Expertise:Skilled professionals with extensive NDT experience.
- 2. Comprehensive Services:Wide range of NDT methods offered.
- 3. Advanced Technology:State-of-the-art equipment for precise testing.
- 4. Dedicated Team: Commitment to thorough and accurate testing.
- 5. Timely Reporting: Prompt delivery of detailed results.
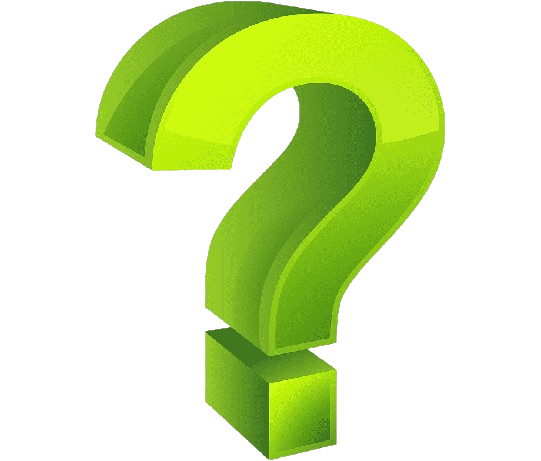